Safety, Articles
Understanding Corrosion Under Insulation (CUI)
Discover the critical issue of Corrosion Under Insulation (CUI) in the oil and gas, petrochemical, and utilities industries. Learn about the causes, impacts, and innovative solutions provided by ARIX Technologies for effective CUI detection and mitigation.

Table of Contents
- Introduction
- Identifying and Mitigating Corrosion Under Insulation
- Advanced Solutions for Corrosion Under Insulation Detection
- Conclusion
- Frequently Asked Questions about Corrosion Under Insulation (CUI)
Introduction to Corrosion Under Insulation (CUI)
Corrosion Under Insulation (CUI) is a severe form of corrosion that affects metallic equipment such as piping systems, pressure vessels, and tanks, which are encapsulated with thermal insulation. This type of corrosion occurs when water or moisture infiltrates the insulation and makes contact with the underlying metal surface, leading to external corrosion beneath the insulation. Corrosion Under Insulation is particularly problematic in the oil and gas, petrochemical, and power and utilities industries due to the extensive use of insulated piping and equipment.
The Impact of Corrosion Under Insulation on Industries
Corrosion Under Insulation (CUI) is a hidden threat that can disrupt industrial operations, leading to costly equipment failures and overwhelming maintenance expenses.
In the oil and gas sector, for instance, CUI can drive up to 60% of piping maintenance costs. This issue contributes to staggering downtime, averaging 32 hours per month—at $220,000 per hour—adding up to a jaw-dropping $84 million annually per facility when predictive maintenance falls short (Senseye, 2022).
Manual inspections, while still common, often fall behind the curve. Around 60% of maintenance professionals admit this approach delays responses to critical equipment issues (Maintenance Technology, 2022). Across production and manufacturing industries, corrosion racks up a $17.6 billion direct cost annually (NACE International). For many facilities, 40-60% of maintenance budgets are swallowed by CUI-related leaks (ExxonMobil Chemical, 2003).
The good news? Integrating advanced technologies, such as robotics, into maintenance strategies has the potential to revolutionize these outcomes, delivering efficiency and cost savings across the board (Deloitte, 2021).
The Science Behind Corrosion Under Insulation
Corrosion Under Insulation primarily affects carbon, low-alloy, and austenitic stainless steel. It is driven by the presence of moisture within the insulation, which can come from environmental sources such as rain, condensation, or process leaks. The insulation materials, design of the piping systems, and environmental conditions all play crucial roles in the initiation and progression of Corrosion Under Insulation.
Key Factors Influencing Corrosion Under Insulation:
-
Insulation Materials: Different insulation materials have varying abilities to absorb and retain moisture, impacting the rate and severity of Corrosion Under Insulation.
-
Environmental Conditions: Temperature fluctuations, humidity, and exposure to corrosive environments can accelerate Corrosion Under Insulation.
-
Design and Installation: Poor design and installation practices can create gaps and crevices where water can accumulate, increasing the risk of Corrosion Under Insulation.
What Causes Corrosion Under Insulation?
Corrosion Under Insulation is primarily caused by the ingress of water or moisture into the insulation material. This can happen due to various reasons, including:
- Rainwater penetration: Damaged or improperly installed insulation can allow rainwater to seep in.
- Condensation: Temperature fluctuations can cause condensation to form under the insulation.
- Leaks: Leaks from nearby equipment or processes can introduce moisture.
- Humidity: High humidity environments can contribute to moisture buildup.
Once moisture is trapped within the insulation, it creates an ideal environment for corrosion to occur, especially in the presence of contaminants such as chlorides or sulfates.
Common Materials Affected by Corrosion Under Insulation
Corrosion Under Insulation can affect a variety of materials used in industrial applications, including:
- Carbon steel: Commonly used in pipelines and vessels, carbon steel is highly susceptible to Corrosion Under Insulation.
- Stainless steel: Although more resistant than carbon steel, stainless steel can still suffer from Corrosion Under Insulation, particularly in chloride-rich environments.
- Aluminum: Used in some insulation applications, aluminum can also be vulnerable to Corrosion Under Insulation.
Identifying and Mitigating Corrosion Under Insulation
Detecting Corrosion Under Insulation is challenging due to the hidden nature of the corrosion beneath the insulation. Traditional inspection methods often require the removal of insulation, which is costly and labor-intensive. However, innovative solutions like ARIX Technologies' robotic inspection systems offer a non-intrusive and efficient way to monitor Corrosion Under Insulation. These robots can navigate through insulated piping systems, providing real-time data on the condition of the metal underneath the insulation.
Mitigation Strategies:
-
Material Selection: Using insulation materials with low water retention and high thermal efficiency can reduce the risk of Corrosion Under Insulation.
-
Protective Coatings: Applying high-quality coatings to the metal surface before insulating can provide an additional barrier against moisture.
-
Design Improvements: Ensuring proper design and installation of insulated systems to minimize water ingress and facilitate drainage.
Advanced Solutions for Corrosion Under Insulation Detection
At ARIX Technologies, we specialize in advanced robotic inspection solutions designed to tackle Corrosion Under Insulation effectively. Our robots are equipped with state-of-the-art sensors and imaging technologies that can detect early signs of corrosion without the need to remove insulation. This innovative approach not only saves time and costs but also enhances the reliability and safety of industrial operations.
Conclusion
Corrosion Under Insulation is a critical issue that requires vigilant monitoring and effective mitigation strategies. By understanding the factors that contribute to Corrosion Under Insulation and implementing advanced inspection technologies like those offered by ARIX Technologies, industries can safeguard their assets, enhance safety, and reduce maintenance costs.
Frequently Asked Questions about Corrosion Under Insulation (CUI)
What is Corrosion Under Insulation (CUI)?
Answer: Corrosion Under Insulation (CUI) is a form of corrosion that occurs when water or moisture penetrates the insulation material, leading to the degradation of the underlying metal surfaces such as pipes, vessels, and tanks. It is often difficult to detect because the insulation covers the affected areas.
What are the primary causes of Corrosion Under Insulation?
Answer: Corrosion Under Insulation is primarily caused by the ingress of moisture into the insulation. This can happen due to rainwater penetration, condensation, leaks, and high humidity. Damaged or poorly installed insulation exacerbates the problem by trapping water against the metal surface.
Which materials are most susceptible to Corrosion Under Insulation?
Answer: Materials commonly affected by Corrosion Under Insulation include carbon steel, stainless steel, and aluminum. Carbon steel is highly susceptible, while stainless steel can corrode in chloride-rich environments, and aluminum can degrade under certain conditions.
How can Corrosion Under Insulation be detected?
Answer: Corrosion Under Insulation can be detected using various non-destructive testing (NDT) methods such as Pulsed Eddy Current (PEC), real-time radiography (RTR), profile radiography, computed radiography, and digital detector arrays. These methods allow for the inspection of insulated equipment without removing the insulation.
What is Pulsed Eddy Current (PEC) and how does it work?
Answer: Pulsed Eddy Current (PEC) is an NDT technique that measures wall thickness loss by emitting an eddy current from an excitation coil towards the object. A time-varying magnetic field is reflected back to a receiver coil, with changes in the magnetic field indicating the presence of defects or flaws. PEC can inspect through insulation without removal and is effective for detecting general wall loss.
What are the advantages and limitations of using radiography for Corrosion Under Insulation detection?
Answer: Radiography provides high-resolution images of the internal structure of insulated equipment. Techniques like real-time-radiography (RTR) and profile radiography allow for the identification of wall thinning and defects. However, radiography can be complex, requiring skilled personnel and specific equipment, and some methods are limited to smaller diameter pipes.
How often should inspections for Corrosion Under Insulation be conducted?
Answer: The frequency of inspections depends on factors such as the operating environment, material type, and history of Corrosion Under Insulation issues. Typically, regular inspections should be conducted annually or as recommended by industry standards and regulations to ensure early detection and mitigation of Corrosion Under Insulation.
What preventative measures can be taken to reduce the risk of Corrosion Under Insulation?
Answer: Preventative measures include proper installation and maintenance of insulation, applying protective coatings to metal surfaces, using moisture barriers and sealants, ensuring good drainage and ventilation, and conducting regular inspections with advanced NDT methods.
What industries are most affected by Corrosion Under Insulation?
Answer: Industries that heavily rely on insulated equipment are most affected by Corrosion Under Insulation. This includes oil and gas, chemical processing, power generation, and marine industries. In these sectors, maintaining the integrity of pipelines, vessels, and other equipment is critical for safety and operational efficiency.
How does the environment impact the occurrence of Corrosion Under Insulation?
Answer: Environmental factors such as humidity, temperature fluctuations, and exposure to chemicals can significantly impact the occurrence of Corrosion Under Insulation. Environments with high humidity and frequent temperature changes are more prone to Corrosion Under Insulation due to increased condensation and moisture buildup.
Can Corrosion Under Insulation be completely eliminated?
Answer: While it is challenging to completely eliminate Corrosion Under Insulation, it can be effectively managed and minimized through proactive maintenance, regular inspections, and the use of advanced detection techniques. Implementing best practices for insulation and moisture control can greatly reduce the risk of Corrosion Under Insulation.
What role do coatings play in preventing Corrosion Under Insulation?
Answer: Protective coatings act as a barrier between the metal surface and the environment, preventing moisture from reaching the metal and causing corrosion. Coatings can be specifically formulated to withstand the conditions that promote Corrosion Under Insulation, enhancing the durability and lifespan of insulated equipment.
Related Resources
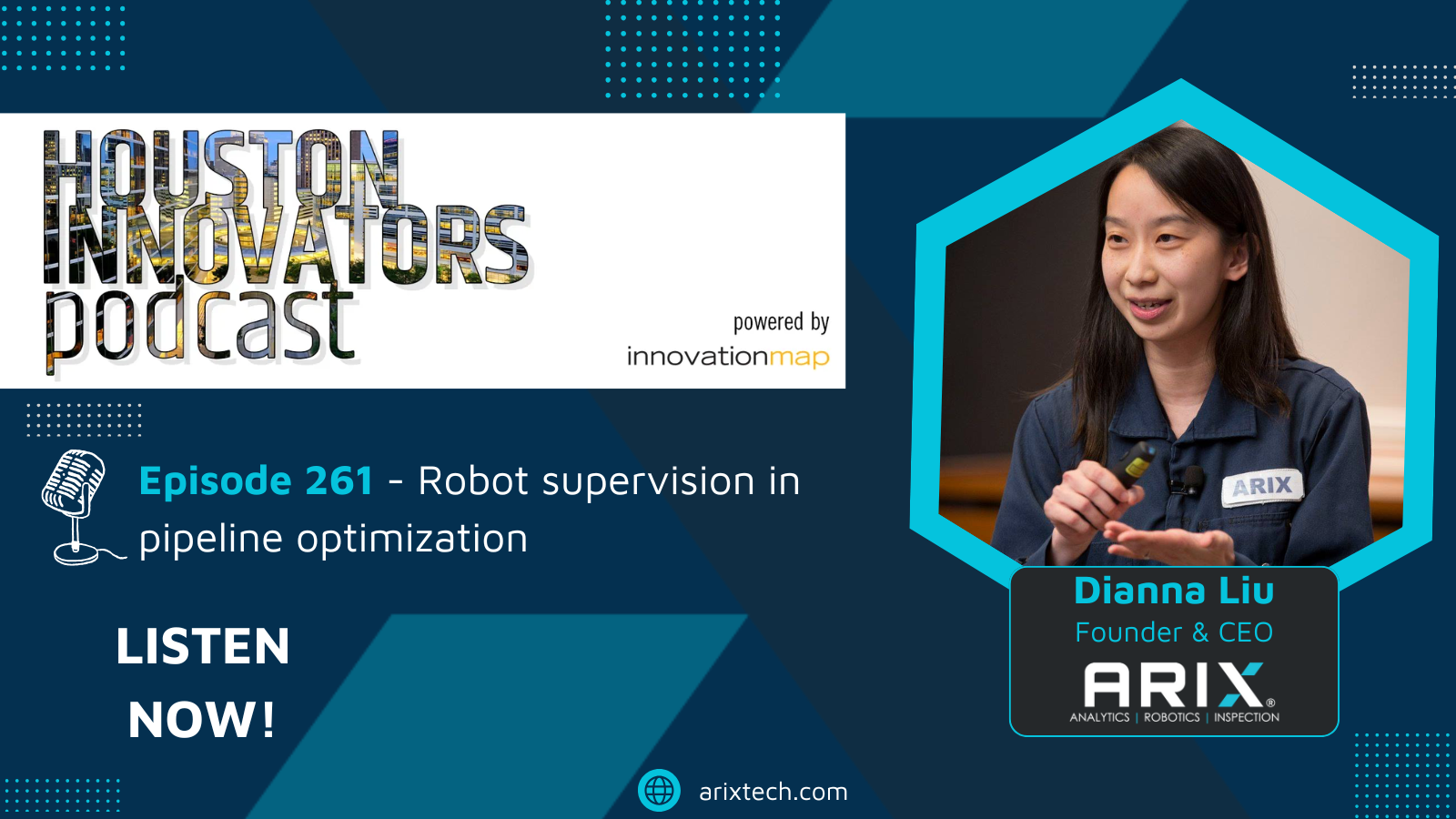
Press, Articles
Dianna Liu Shares Vision on the Houston Innovators Podcast
ARIX founder Dianna Liu shares her journey from downstream energy to robotics, transforming pipeline safety. Listen now.
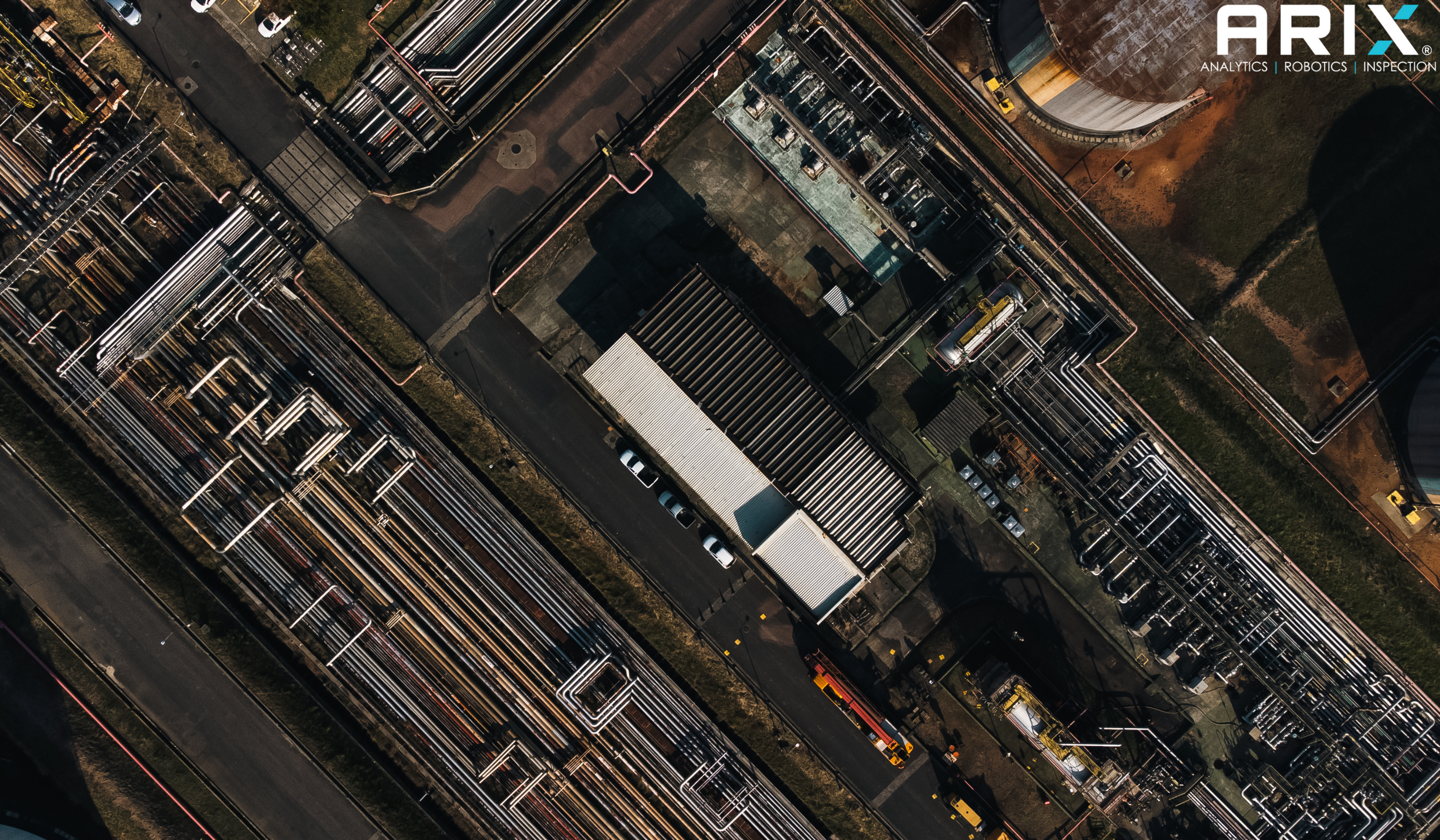
Safety, Articles
Founder Interview: Robotic Solutions Are Transforming Inspections
Discover how ARIX Technologies uses robotic pipeline crawlers to enhance safety, reduce costs, and improve the efficiency of corrosion inspections.
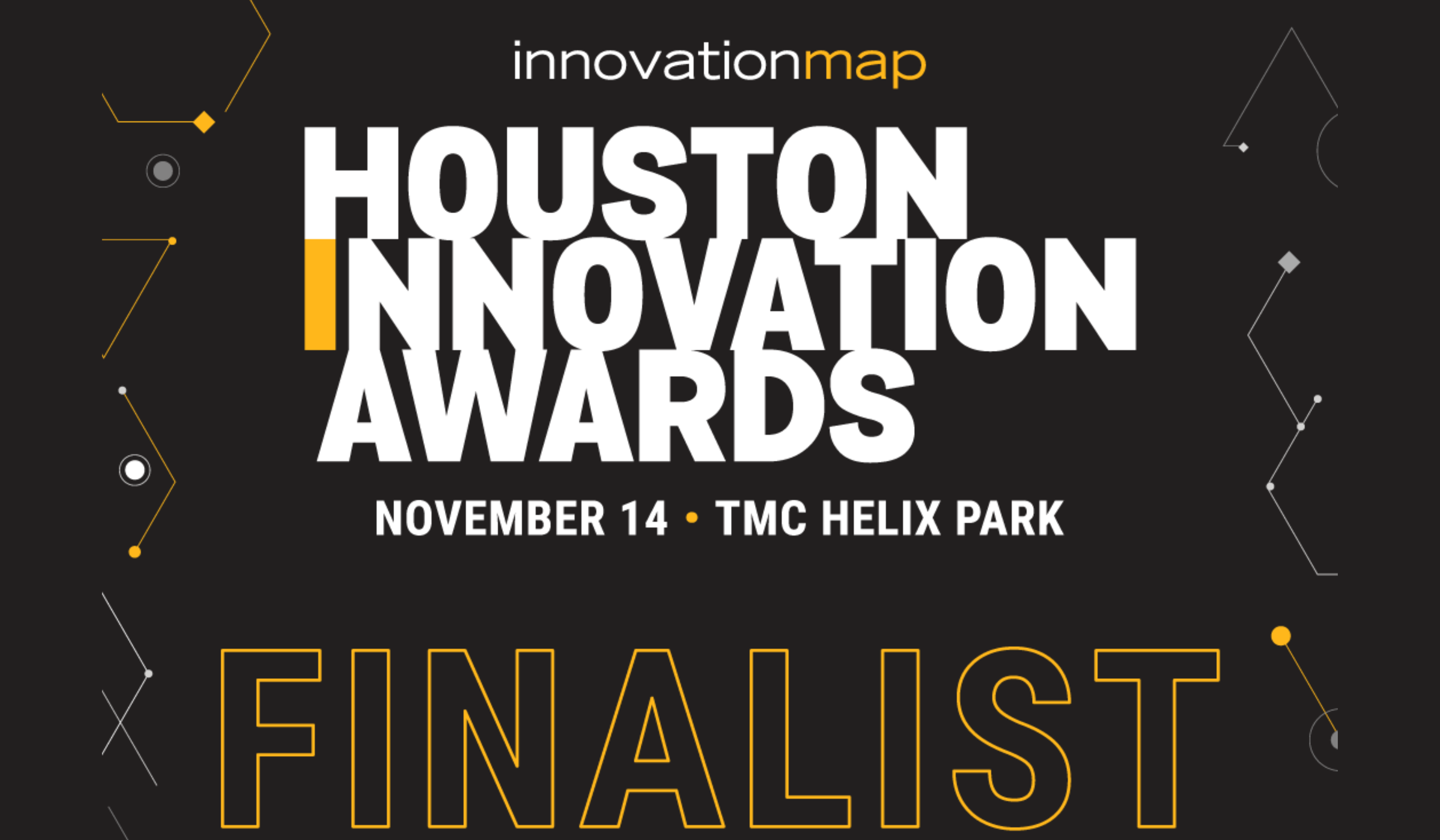
Press, Articles
ARIX Named Finalist for 2024 Houston Innovation Awards
ARIX Technologies has been named a finalist for the 2024 Houston Innovation Awards in Energy Transition and AI/Data Science.
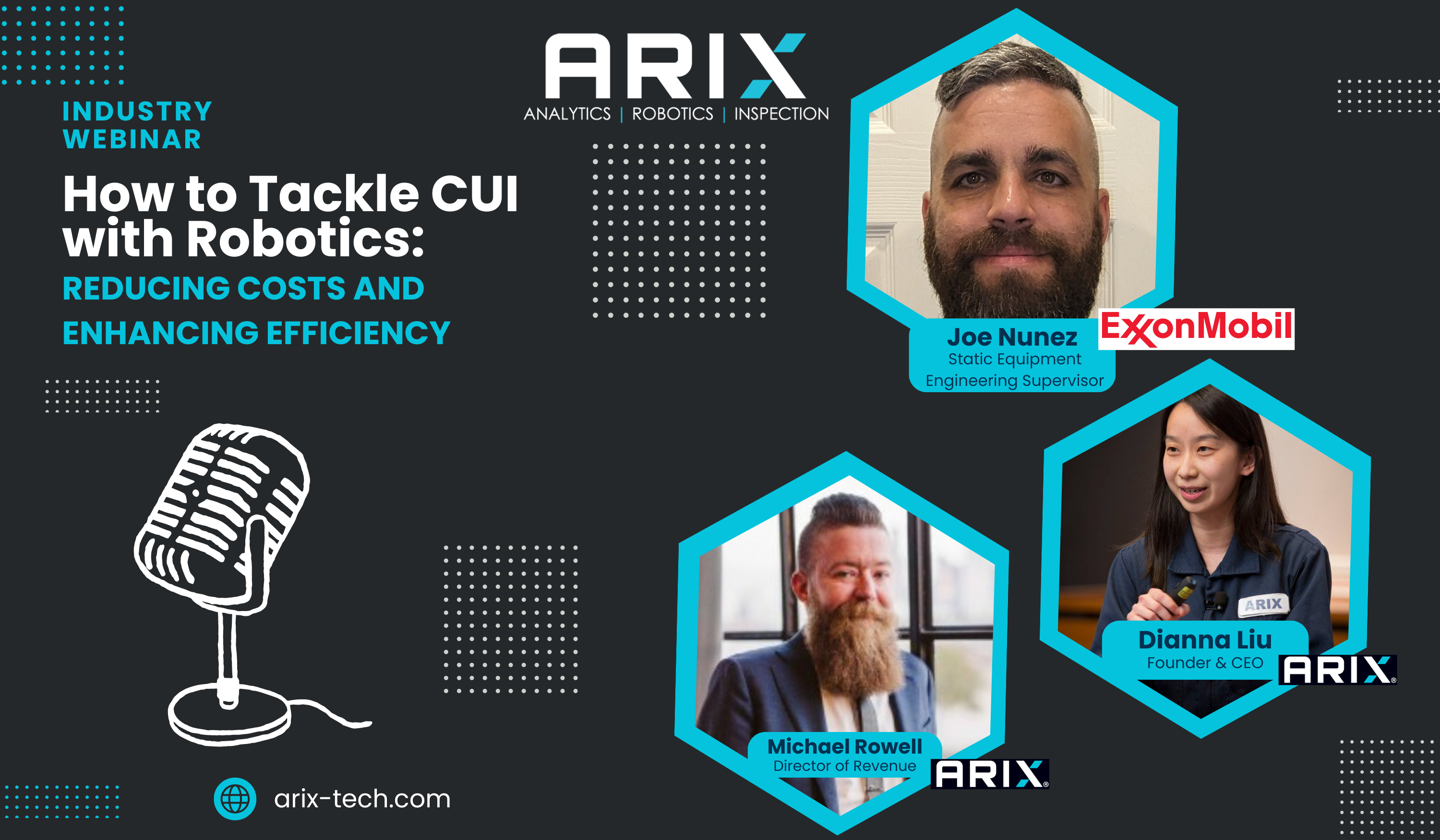
Videos, Articles
How to Tackle CUI with Robotics: Reducing Costs & Enhancing Efficiency
Discover how robotics and advanced inspection techniques like Pulsed Eddy Current (PEC) are revolutionizing refinery inspections and corrosion detection. Learn from industry experts how these innovations enhance efficiency, reduce costs, and improve safety.
Get in touch with us!
Want innovative solutions to increase safety, lower costs, and preserve your equipment for years to come?
Let’s Talk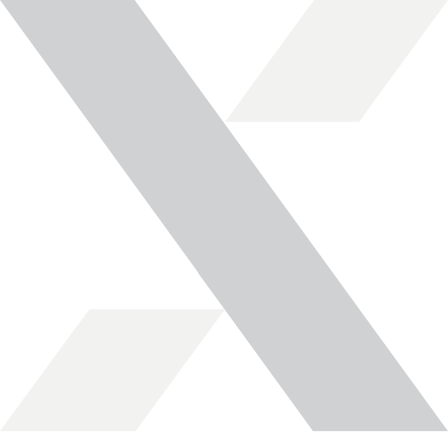
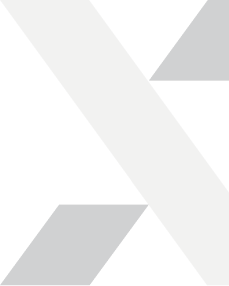